Process Improvement and Innovation
Significance
‘Innovation’, in the context of Banpu Power, is the design and selection of high-efficiency and clean technologies suitable for each project , and the initiation to change the working process to be more efficient. This can be proceeded through studying how to improve the procedures, probably including applying advanced technologies to current tasks. The development of production processes and innovations are major factors in increasing competitive advantages, especially using digital technology in the production process, supply chain management and energy trading.
Management Approach
With an aim to increase workforce efficiency and process reliability, as well as to reduce costs and losses in a production process, BPP has improved its production efficiency based on the principle of “Operational Excellence” together with innovations through participation of employees at all levels. By this means, all employees collaborate to identify problems possibly arising during work, find the root causes through a systematic process, and make improvements continuously. This operating process starts with training employees to enable them to identify the problems possibly arising during working processes with supports from a corporate team. Moreover, a knowledge exchange between business units for mutual learning has been conducted, while employees have the opportunity to present the projects initiated and implemented with fruitful results.
BPP drives innovations through a creation of corporate culture – the “Innovative” value, which is one of the three corporate shared values. Innovation has been promoted through various activities to make all employees understand the importance of applying innovation to their works. BPP encourages its employees to present ideas and innovations in order to turn those initiatives into tangible practices. It also promotes learning within the organization in the form of a “Learning Application Project”, encouraging employees from different departments to work on projects together, by using creativity and innovation. The project initiated, then, will be presented to the committee to approve on budgets for operation.
BPP has set up the “Innovation Committee”, comprised of employee representatives, who are responsible for promoting innovation within the organization. In addition, knowledge management and an annual “Innovation Convention” have been conducted to transfer innovation knowledge within the organization. The annual “Innovation Convention” aims to exchange knowledge, and experiences, as well as to demonstrate the outstanding performance of employees in implementing innovative projects.
BPP has employed a mechanism to screen production development projects, innovations, and various digital projects thoroughly, by setting evaluation criteria covering the areas of investment values, risks, financial returns, and environmental, social, and governance (ESG) factors, as well as sustainability. This includes expanding the projects for implementing in other production units.
Due to its awareness of future operations, in which digital technology will play an important role in creating competitive advantages, and in according with the “Greener & Smarter” strategy, Banpu Group places great emphasis on the transformation of work processes towards the digital age (Digital transformation). In addition, a selection of technology and a development of information systems must be suitable for 1) a level of business necessity 2) meeting the objectives, and 3) having opportunities to realize the returns quickly. Meanwhile, the infrastructure laid down must be highly flexible to support business expansion. More importantly, a system to prevent cyber security risks has been installed since a power business is a security part in the area possibly being a target for cyber threats. As a result, a risk assessment is required, while a safety must be tested. Furthermore, preventive measures have also been established to be always up-to-date, while a Global Information Security Officer (GISO) has been employed with duties on and responsibilities for supervising information security, digital technology risks, and legal compliance across Banpu Group.
Performance
- Combined heat and power (CHP) plants recorded AF of 95.98%, and FOF of 0%.
- Gas-fired power plants had AF of 82.68%, and FOF of 0.51%.
- Overall cybersecurity and privacy maturity score was 3.5.
- Bangkok Office and Beijing Office were certified ISO 27001:2013 Information Security Management Standard.
- Conducting a business continuity plan (BCP) drill in order to test a response plan in the event of business and personal data leakage.
Key Activities and Projects
As digital technologies have drastically been reshaping the way we live and work, digital transformation has been on Banpu group and BPP’s agendas as one of the key success factors to drive its business transition aligned with the Greener & Smarter strategy.
To reflect the progress of Banpu group’s digital transformation journey, starting since 2018, Banpu Group assessed its digital, automation, industrial-internet-of-things (IIoT) and analytics maturity at a group level. Four areas of management best practices were measured, including
- strategy
- corporate culture
- right structures and internal processes, and
- digital skills and technology capabilities.
The assessment, which was done by leveraging a third party self-diagnostic tool from one of the globally leading digital consulting companies, helped the company to discover digital opportunities as well as identify gaps between current capabilities with the final goal of becoming a leading digitally driven organization. The methodology has a proven track record and has been used by more than 550 companies across multiple industries globally. More than 80 energy, gas, and mining companies were used in the benchmarking.
At the asset level, Zhengding CHP Plant became the first CHP plant in China to be assessed by using the Smart Industry Readiness Index (SIRI), created by the Singapore Economic Development Board (EDB) in partnership with a network of leading technology companies, consultancy firms, and industry and academic experts. SIRI is comprised of a suite of frameworks and tools to help manufacturers – regardless of size and industry – in starting, scaling, and sustaining their manufacturing Industry 4.0 transformation journeys. Zhengding CHP Plant has shown the areas for improvement in only 4 out of 16 dimensions of the SIRI framework, which now helps identify the development priorities for the operations.
Accelerating digitization by using low-code platforms:
User-designed applications using low code platforms such as Microsoft PowerApps and Microsoft Power BI are the instruments for increasing the digitization of business processes across Banpu Group. These applications provide structured data for further analytics, visualization, and decision-support, which was previously impractical or inefficient.
Robotic process automation, cost-effective IIoT networks linked to cloud data platforms and visualization tools are enabling us to drastically improve the efficiency and accuracy of the collection, analysis and reporting of environmental, social and governance (ESG) information from the front-line operators to stakeholders. The applications BPP has used in many cases include:
- Blink: an application for collecting sustainability data and reporting;
- IRIS: an application for market intelligence of coal supply chain; and
- ENIGMA: an application for BPP asset monitoring dashboard, focusing on renewable energy generation assets.
People transformation enabling home-grown agile digital studio:
The importance of digital and transition to tech-enabled work environments is everywhere across the globe. More importantly, attracting and retaining people with right capabilities and talents will continue being a growing challenge in all business domains. Up-skilling and re-skilling existing workforces deeply understanding the company’s culture and having hands-on experiences in the functional business process is the key factor to sustain the transition to the workplace of the future.
HPC Power Plant in Laos successfully completed Phase-1 of its boiler improvement program, focusing on reconfiguring and deep analytics of data from the existing acoustic sensors. The whole process, starting from diagnostics to prioritization, workstream planning and execution, was done by an energetic inhouse team whose achievement we are proud of. Besides, Phase-2 will activate prediction capabilities or the system and lay down the foundations for building digital-twins of mission critical equipment.
Going Forward:
The transition pathways to a low-carbon, clean and green world will remain at the core of all business strategies in the years to come. With the Greener & Smarter strategy taken place since 2015 and the Digital Transformation program executed since 2018, Banpu Group has been well positioned in focusing its transformation efforts and agile change on decarbonization of our energy value chains as well as bring step-change improvements in operational safety of all our assets and operations and the communities.
Our network of Digital Capability Centers (DCC) at Beijing and Luannan Power Plant act as the innovation and ecosystem engagement hubs to continue our journey towards a digitally enabled enterprise.
We will continue the re-skilling programs through Banpu Digital Academy (BDA) and improving the way our people collaborate with each other under the digital environments via the constant user experience and user interface (UX/UI) design improvements, as well as pursuing new growth opportunities by commercialization of relevant digitized cases to other industry peers.
Example of courses offered by BDA: Scrum 101, Design Thinking, Creativity, Design Thinking and Innovation for Business, New Lean Startup Principle, Product Management Fundamental and Introduction to Business Analytics.
BPP has implemented innovation projects with an aim to create competitive advantages, improve performance and stability in the long-term. Due to production process improvement and innovation implementation in the last year, the availability factor (AF) and the forced outage factor (FOF) of power plans, in which BPP has management control, met the target set. The power plants were able to operate their production efficiently and stably according to the target, for examples.
- The “waste heat recovery from utilizing de-white facility” project implemented at Luannan CHP Plant.
- The thermal energy conservation for maximum efficiency project, conducted by Zhengding CHP Plant.
- The project to increase production availability of Temple I Power Plant.
- The Advanced Leakage Monitoring and Alerting Software (ALMA) project.
- The project to increase boiler’s combustion efficiency of HPC Power Plant.
- Structural Improvement of Water Pump Station in the Demineralization System to Prevent Damage Caused by Extreme Weather Conditions of Temple Power Plant.
- Improving Power Generation by Installing an Auxiliary Transformer Cooler System.
- Increasing an Accuracy of Power Generation Forecasts by Installing a SkyCam Forecasting Device.
- Boiler Examination Through Risk Base Inspection (RBI).
- The data security system and risks were inspected by an external consulting agency to look for improvement opportunities. BPP and Banpu Group received an overall score of 3.5 points (against a full score of 5), up from 3.0 in the previous year due to measures’ improvements to prevent and solve cyber risks resulting from suppliers’ operations (Third-party risk).
- Conducting a business continuity plan (BCP) exercise to test a responsive plan, in the event of business and personal information leakage. Objectives of BCP exercise were as following:
- To test relevant incident response plans and business & personal data leakage plans.
- To review and understand the concept, roles and responsibilities of involved employees.
- To examine internal communication effectiveness.
- To measure, analyze, and evaluate in accordance with the ISO 27001:2013 requirements
- Adopting the ISO 27001 Information Security Standard System to help in strengthening data security management, reducing risks, and protecting data from thefts in the Bangkok and Beijing offices. It is in the process of studying the possibility of expanding the scope to a CHP plant.
Digital technology is one of the key success factors in driving business transformation in accordance with “Greener & Smarter” strategy. Therefore, Banpu Group has embarked on Digital Transformation since 2018, by establishing a digital development department to drive the organization towards a digital era completely.
Currently, BPP has operated various power generation businesses in China, including combined heat and power (CHP) plants, and solar power plants, which are joint-venture companies. Since each business unit was established at a different time, they are different in terms of technology used in production processes, machineries, and equipment. These cause employees to spend much time collecting and analyzing data to be used in management and making decisions, both at the operational level and overall management. Moreover, the applications available in the market are not up to the mark and are expensive.
BPP is able to enhance digital competencies of operating staff and engineers in business units, who have expertise in various fields in the power business, including building upon more advanced digital skills, such as data science, data analysis, and data-visualization. This will lead to development of BPP’s digital projects according to the “Greener & Smarter” strategy.
Presently, 8 employees in China have been developed their capabilities and are equipped with digital skills necessary to help drive over 70 digital projects in the future. This drive stems from a continuous creation of the “Innovation” corporate culture for a long time. Until now, the “Innovation” corporate value is recognized by local stakeholders and the government sector.
HPC Power Plant has developed a software to monitor and alert leakages in its boiler tubes in order to have enough time in preparing a repair work in advance, and to reduce revenue loss from unplanned production stoppages.
The ALMA software has adopted digital technology in the field of artificial intelligence (AI) to help detect leakage in boiler tubes. This makes it possible to recognize the leakage signal faster than usual. The software model was developed from statistical data of machineries and other related information, such as audio detection, and a make-up water consumption. After that, the ALMA system will send an alarm signal to the production personnel, enabling the power plants to make decisions on maintenance plan in advance, including being able to reduce the loss and prevent it from spreading more.
The software development has received collaboration from one employee of the Boiler Maintenance Department of HPC Power Plant, three production and maintenance contractors, four employees from BPP and Banpu Group, together with external consultants. From the operation, it was found that the leakage in boiler tubes could be notified 3-5 days in advance, which gave the power plant plenty of time to prepare for a repair work, and reduced a loss from fines due to the power plant’s notification on immediate and unplanned production halt. Such a production halt costs about THB 5 million per time or about THB 14.4 million per annum (This information is from statistical data during 2021-2022). Moreover, this software has a function to improve its model to be more accurate in the future.
Document Download
Innovation Policy
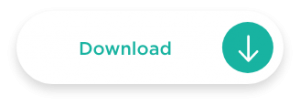